Steps to Bring your Project to Life
The Process

Design and onboarding
We’ll sit down with you and review your design and project scope and goals. We’ll help you refine your design and your CAD files to assure the manufacturability at the most economical cost. We ensure there is a plan in place to make the manufacturing process seamless.
Materials selection
Our experts will help you choose the right plastics for your job. We want you to be happy with both the function and aesthetics of the final product.
Tooling
We create a mold from your design. Depending on the volume and complexity, various medias are looked at for tooling, ranging from wood and epoxy boards to fabricated or cast temperature-controlled aluminum. When fabricating your mold, our goal is to include as many individual parts into the mold as we can, to reduce the end cost to our customers.
Thermoforming
When the mold is complete, it’s time to bring your project to life. We heat the plastic chosen for your job to a pliable temperature and then use vacuum and possibly air pressure to shape the plastic to your mold. Once the plastic has cooled, we remove from the mold and trim any excess material.
Value added assembly
Often times after a customer’s plastic project is thermoformed and trimmed, the design requires additional assembly services. We offer a plethora of secondary manufacturing options so you can work with a single partner to bring your project to life.
What are the advantages of Thermoforming?
Custom Thermoforming vs Injection Molding:
Custom thermoforming has a much lower initial tooling cost than other plastic processes, like injection molding. Quick turn prototypes in an economical fashion.
Custom Thermoforming vs Sheet Metal Fabrication
Custom thermoforming has a much lower initial tooling cost than other plastic processes, like injection molding. Quick turn prototypes in an economical fashion.
Types of Thermoforming Offered at Bo-Mer
Our customers are who make us a success. We’ve been fortunate to work with some fantastic minds in the innovation and manufacturing industry.
- Vacuum Forming
- Pressure Forming
- Drape Forming
- Membrane Press Forming
- Free Forming
Our Thermoforming Equipment
Rotary Thermoforming Machines
Can accommodate up to a 6’ x 10’ x 41” depth.
Single Station Thermoforming Machines
Can accommodate up to a 7’ x 11’ x 40” depth.
Inline (thin gauge) Thermoforming Machines
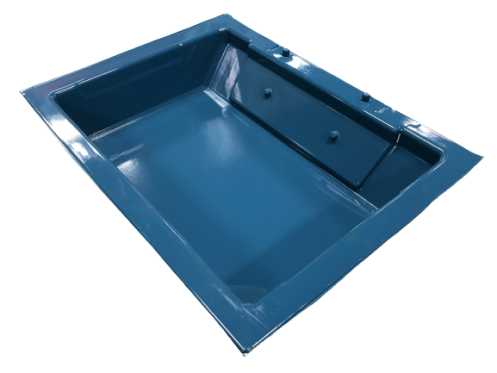
Project:
Pressure formed cover
Thermoforming Gallery
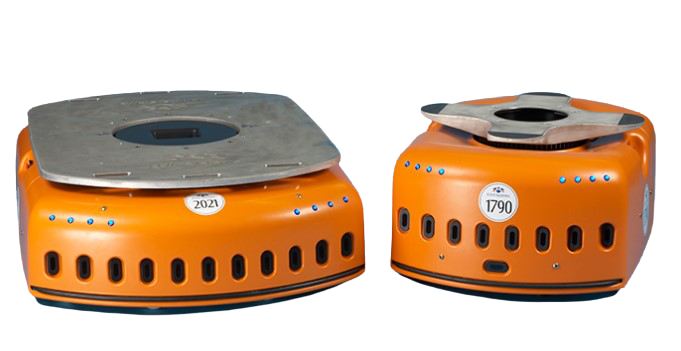