Experts in Custom Thermoforming, Rotational Molding and Sheet Metal Fabrication
Our Services
Bo-Mer delivers cutting-edge services across diverse industries, catering to everyone from major corporations to local mom-and-pop shops. No job is too big or too small for our expert team.
Custom Thermoforming
Thermoforming is a process where an extruded sheet of plastic is heated to a specific forming temperature, formed to the shape of either a female or male mold and then trimmed to fit the desired, detailed finished product. It involves far less tooling and investment than other plastic molding processes, making it an advantageous means of production.
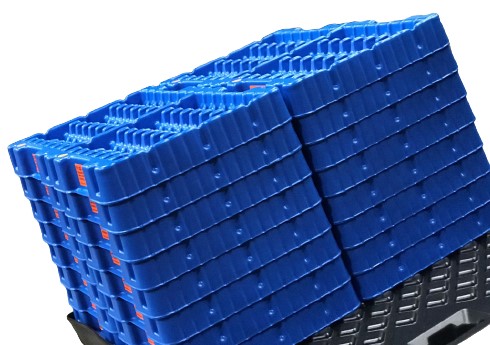
Vacuum Forming
Bo-Mer has been striving to find the most effective ways to serve our customers since 1946. This is where our vacuum forming services come into play. By providing this option for our customers, we can offer lower costs and faster results, due to superior production variables.
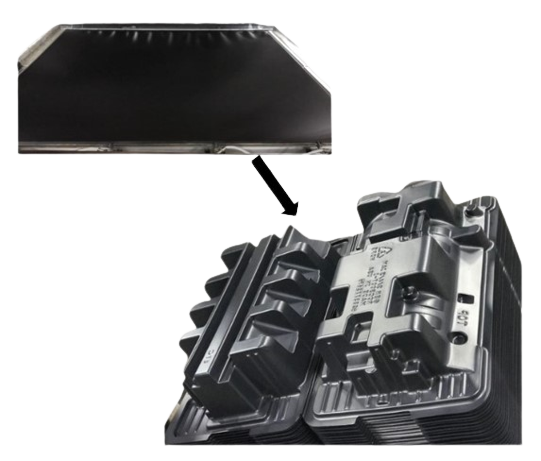
Pressure Forming
Pressure forming is a more advanced form of vacuum forming. The mold creates the desired shape with the force of a vacuum on one side of the sheet and compressed air pressure on the other. Pressure forming can produce the fine detail that injection molding can, however it is done at a fraction of the cost.
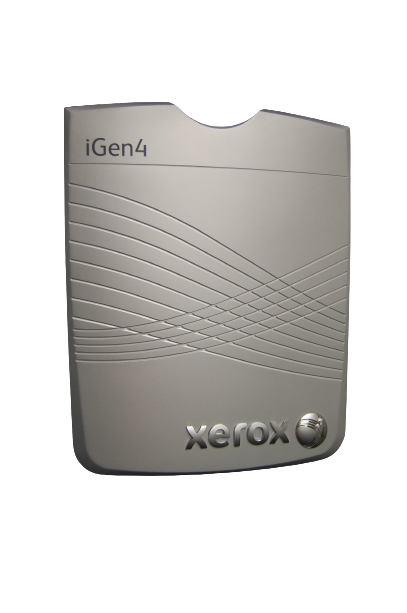
Membrane Press Forming
Membrane press forming may be considered a type of “drape” forming, however this process requires the use of a vacuum. In our case, we heat a sheet of material, drape it over a mold which is usually made of wood, epoxy, or aluminum and then a vacuum is pulled between the mold, which has the material and the membrane on it. As the vacuum is pulled, the membrane is able to push the material in the configuration of the mold.
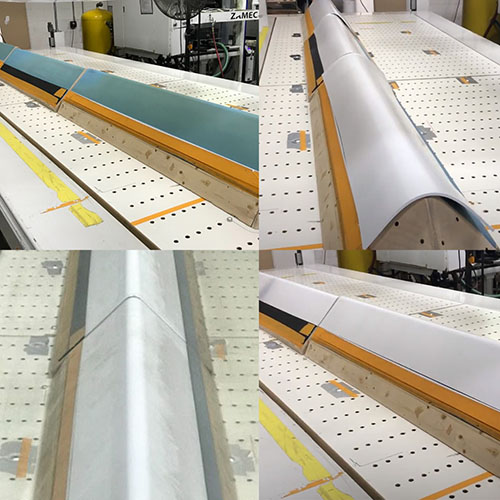
Drape Forming
Unlike most thermoforming processes, drape forming does not stretch the plastic during the formation of the part. A sheet of heated extruded plastic is manually draped over a mold to create the desired shape without the use of a vacuum. The mold is usually a felt lined wood or epoxy board with a matched upper and lower “clamshell” type of mold.
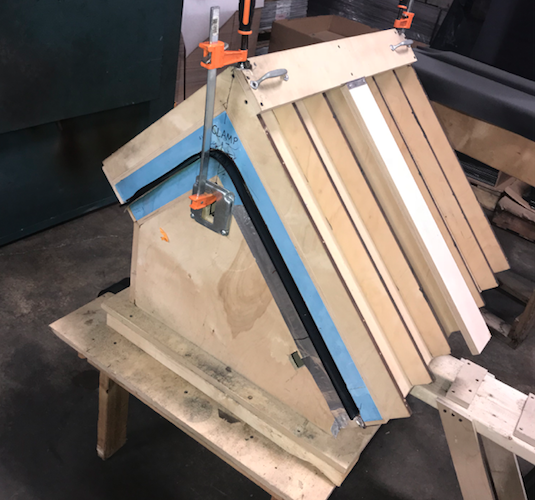
Free Forming
We tend to use the free forming process on jobs that call for the clarity of the product to be a top priority. This process allows us to concentrate on the clarity of the material because the material never actually touches the mold as it is formed, it is sucked down into an open mold by a vacuum to its desired shape.
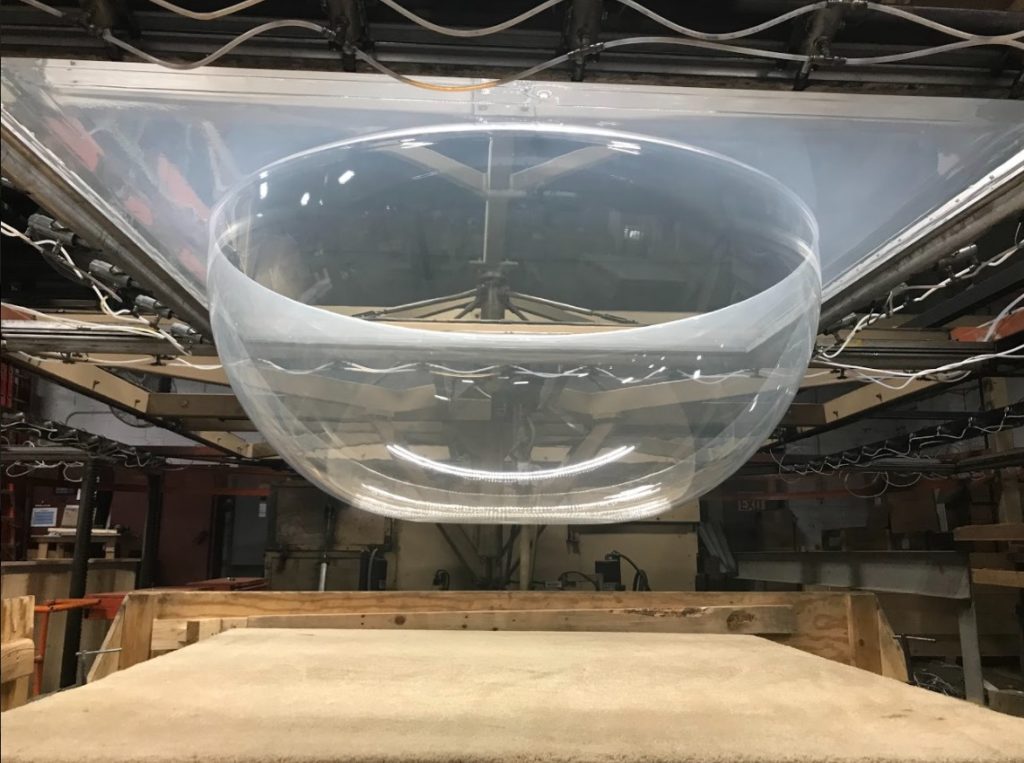
Plastic Fabrication
A value-added process that we offer in-house which gives us the ability to create plastic and/or metal structures, parts and machines from a variety of raw materials. Because we have the ability to fabricate without outsourcing, we offer additional value to our customers by reducing the number of vendors that are needed to complete different services, reducing the overall cost.
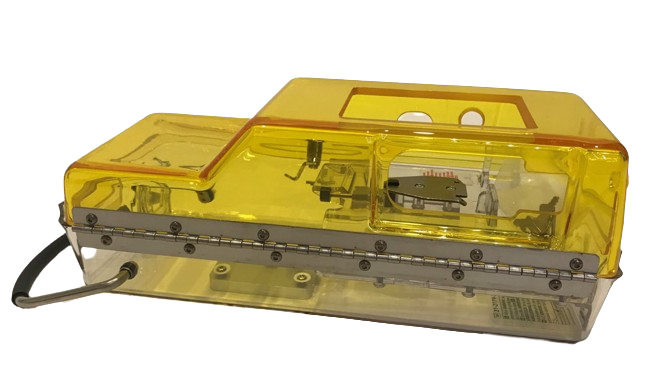
Rotational Molding
Rotational Molding is a manufacturing process where a heated hollow mold is filled with a precise amount of resin. The mold is then bi-axially rotated in an oven, allowing the material to soften and evenly coat the mold’s interior walls. The speed and rotation are crucial for achieving consistent thickness throughout the part. This rotation continues during both the heating and cooling phases, ensuring optimal material distribution and quality in the final product.
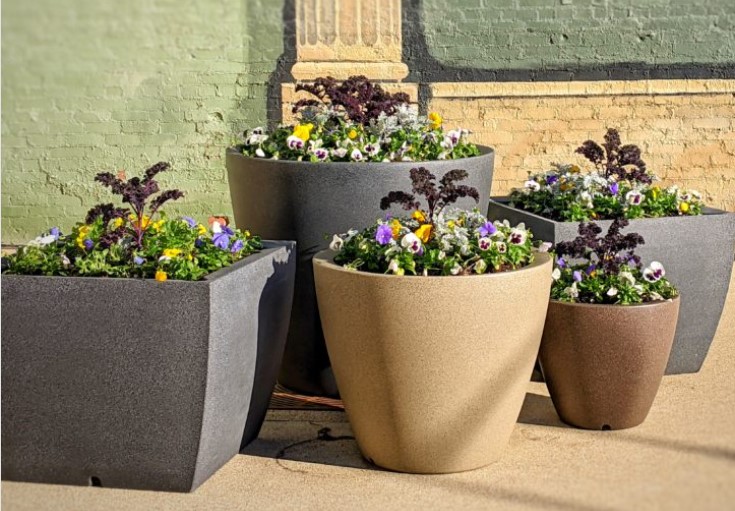
Metal Fabrication
A value-added process that we offer in-house which gives us the ability to create plastic and/or metal structures, parts and machines from a variety of raw materials. Because we have the ability to fabricate without outsourcing, we offer additional value to our customers by reducing the number of vendors that are needed to complete different services, reducing the overall cost.
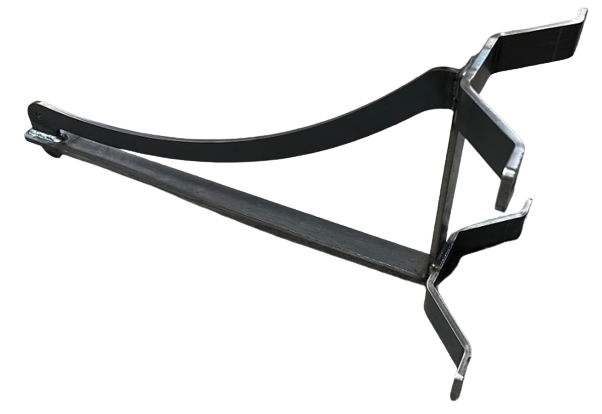
Painting
We provide painting to offer extra value and service to our customers.
- Solvent Based
- Water Based
- EMI/RFI Shielding
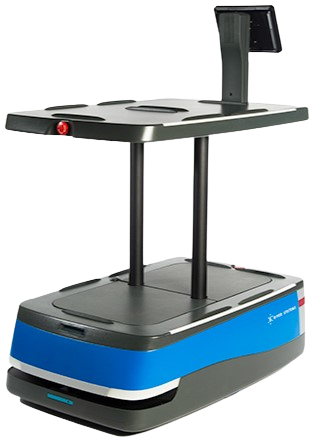
Full Assembly
We provide a full assembly of services to offer extra value and service to our customers.
- Assembly of plastic & metal components
- Welding / laser welding
- Adhering, riveting, eyeleting, sewing, soldering
- Painting & EMI/RFI shielding
- Screen printing & powder coating available via reliable outsourcing
- 3D printing
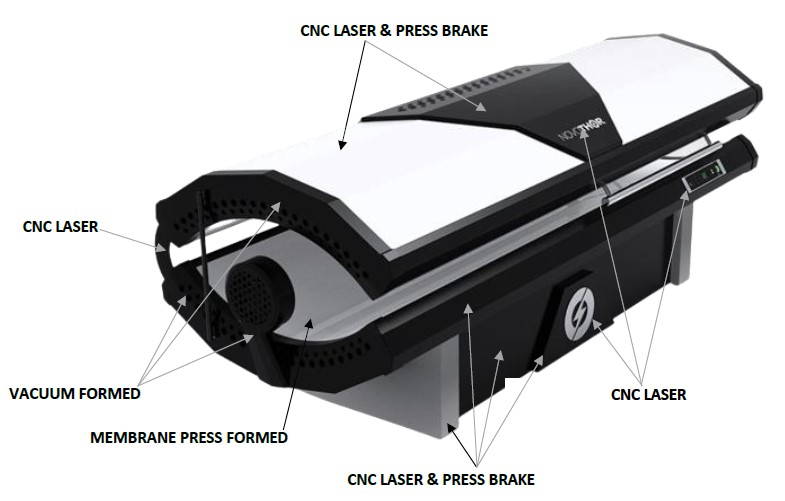
“…you are definitely on the list of ‘amazing vendors we need to do more work with.’ I’ll certainly spread the word that you are the only choice for domestic thermoforming.”
Leading US Robotics Company
Our Customers, the Visionaries
Our customers are who make us a success. We’ve been fortunate to work with some fantastic minds in the innovation and manufacturing industries.
Featured Project
Bo-Mer Plastics offers an insight to some of our products, where we show you step by step of what it looks like to bring our customer’s projects to life.
Project:
Medical Device Cover
Service
Thermoforming
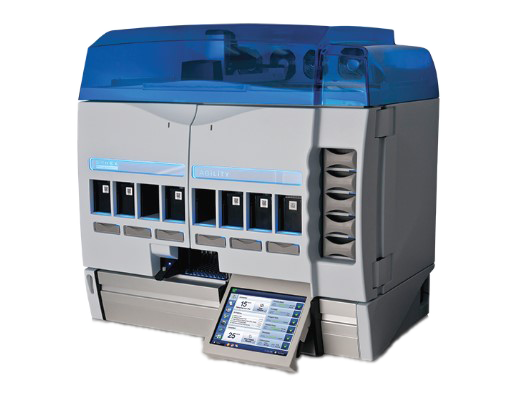
In this video, we take a look at our thermoforming process for manufacturing a medical device cover from a single sheet of PETG plastic. Our vacuum forming process in conjunction with 5-axis trimming techniques and value-added services allow us to create large, complex, and unique shapes while minimizing material waste.
Values We Live By
Never Say Never Approach
When others say it can’t be done, we’re busy getting it done.
Engineering & Manufacturing
Expertise across all disciplines.
Unmatched Quality & Service
It’s a part of our DNA.
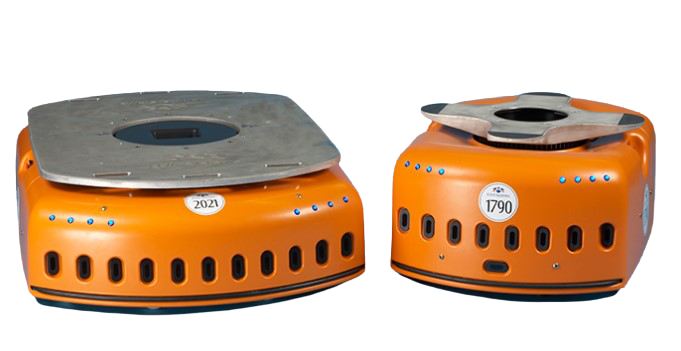